Even though there has been a lot of change in the jewelry design industry, the chainiste occupation is still highly regarded. Handcrafted metal chains, especially those of precious metals like silver and gold, are the specialty of a highly trained artisan known as a chainiste. Using methods that have been handed down through many generations, their work combines innovation, accuracy, and tradition. In addition to adding to the aesthetic value and practicality of jewelry, chainistes also increase its longevity and ease of use. This article delves into the chainiste’s crucial role, the techniques they use, and the significance of their craft in contemporary luxury goods.
What is a Chainiste?
An expert in the art of making and assembling metal chains, usually for use in expensive jewelry, is known as a chainiste. Their specialty is creating elaborate chains from individual links, which are typically crafted from precious metals like gold or silver. Attention to detail and high-quality craftsmanship are hallmarks of chainistes’ work, which guarantees a product that is both beautiful and long-lasting.
While chainistes used to be primarily responsible for making chains by hand, new technologies have given them more duties. Modern chainistes produce chains in large quantities using sophisticated mechanical processes for a wide range of products, from high-end fashion accessories to tools and machinery. This change has not diminished the importance of the craftsmanship and skill needed to design unique chains for demanding customers.
The Role of Chainistes in Jewelry Design
Working closely with designers, chainistes craft chains that are both practical and visually stunning, playing a crucial role in the jewelry-making process. Crucial to the finished product is their mastery of metalworking, material science, and the art of manipulating these elements to fashion long-lasting and aesthetically pleasing chains.
Mastering the Craft of Chain Making
Understanding Materials in Chain Crafting
Although chainistes work with a wide range of materials, the most popular metals utilized by them are gold and silver because of their durability, pliability, and sheen. Particularly when making chains, it is important to take into account the different qualities of the various types of gold, which include yellow, white, and rose gold. The unique problems that come with silver include tarnishing, which necessitates extra care when working with the metal if you want it to retain its luster.
Techniques Used by Chainistes
There are a lot of complicated steps involved in making a chain. It is common practice for chainistes to start by making the individual links and then joining them using techniques like soldering or welding. To make a smooth and consistent chain, the links should all be the same size and shape. Because each link is hand-inspected for strength and aesthetic appeal before being added to the chain, handcrafted chains often require hours of labor.
Durability and Strength of Chains
Maintaining the work’s longevity is an important part of a chainiste’s job. Chains, particularly those employed in exquisite jewelry, are expected to endure everyday usage while maintaining their shape and allure. The accuracy of the soldering process is just as important as the material used to determine a chain’s strength. The usefulness and value of chains are diminished when they are poorly made because they break easily.
Designing Bespoke Chains for High-End Clients
Bespoke chains are one-of-a-kind pieces of jewelry that are designed and manufactured according to each client’s unique specifications. In order to create one-of-a-kind chains that mirror each client’s individual taste, chainistes frequently collaborate closely with their customers. During this step, you can decide on the chain’s overall length and thickness in addition to the material and link style. Bespoke jewelry is a work of art for high-end customers because of the meticulous craftsmanship and unique design that goes into each piece.
Preserving Traditional Chain-Making Techniques
While mass-producing chains has become much easier with the help of modern machinery, many chainistes continue to use time-honored methods that have been handed down through many generations. Luxury jewelry is still largely handcrafted because many customers value the uniqueness and quality of such pieces. In order to keep the cultural heritage of jewelry-making alive, it is crucial to have chainistes who can preserve these traditional methods.
The Evolution of Chainistes in the Modern Era
Over the past few decades, the chainiste’s function has changed dramatically. Technological advancements have given these craftspeople new avenues to explore, even though the fundamentals of chain-making have not changed.
Incorporating Technology in Chain Manufacturing
Advanced Machinery and Tools
Modern machinery is often utilized by chainistes in today’s fast-paced world. Cutting and soldering links are two processes that these machines can automate when making chains. The skill of a chainiste is still necessary to make designs that are unique for the high-end market, even though machines can boost productivity and output.
3D Printing and Digital Design
The incorporation of 3D printing technology is a relatively new development in the field of chain manufacturing. These days, chainistes can use digital tools to create prototypes of their chains before investing in the real thing. When compared to hand-drawn designs, this process offers more precision and flexibility, making it ideal for complex patterns. Additionally, it helps chainistes better serve their customers by reducing the production time for customized items.
Mass Production for Commercial Brands
A new role for chainistes has emerged in the commercial mass production of chains brought about by the emergence of global fashion brands. Many well-known jewelry brands employ chainistes to keep an eye on the production process and make sure the chains are up to par. The skill of a chainiste is still essential, even though the emphasis is on reliability and longevity rather than on individual attention to detail.
The Importance of Durability in Chain Making
Ensuring Long-Lasting Quality
Chains, especially those intended for daily wear, must be designed with durability in mind. A chainist’s skill lies in their ability to increase a chain’s strength without lowering its aesthetic standards through the careful selection of materials and methods. For instance, while a thicker chain could withstand more wear and tear, its luster may be compromised. To make something that serves its purpose and looks good doing it, you need to strike a balance between these two aspects.
Testing Chains for Wear and Tear
To make sure a chain can handle everyday wear and tear, it goes through extensive testing before it reaches the customer. In order to determine how well their creations hold up under stress, chainistes frequently pull or twist the chain. Ensuring the chain will endure for years to come, this testing process helps prevent issues like broken links or weakened connections.
Soldering and Link Security
The strength of a chain is directly related to the skill of soldering, making it one of the most important aspects of chainmaking. Because a broken chain can be the consequence of a weak solder, chainistes pay great attention to this stage of production. In order to avoid any potential weak spots in the chain, it is imperative that the links be fastened securely, particularly in pieces intended for fine jewelry.
The Chainiste Profession in the Luxury Market
When it comes to their high-end jewelry collections, luxury brands frequently commission chainistes to craft unique chains. These craftspeople add an air of mastery to the brand’s wares, elevating them above mass-produced jewelry.
Working with High-End Clients
Custom Chain Designs
Crafting unique chains that embody each client’s unique style and taste is a common practice for chainistes who work with high-end clients. Customers can put their own unique spin on these items by choosing the fabrics and details that speak to them. Due to the meticulous nature of the work involved, a custom chain can take several weeks—if not months—to complete.
Collaborations with Designers
Working together, famous jewelry designers and chainistes often realize their dreams. It is the chainiste’s job to meticulously craft the designer’s vision, even though the designer may have a general idea of what the final product should look like. Some of the most beautiful and desirable jewelry pieces in the world are created through these partnerships.
Maintaining High Standards
Chainistes are required to follow stringent quality control standards because their high-end clients demand nothing less. Iterative quality control ensures that the final product is error-free before it is sent to the customer. What differentiates high-end jewelry from mass-produced items is the meticulous attention to detail.
FAQs
What is a chainiste?
A chainiste is a skilled artisan who designs, crafts, and assembles metal chains, often used in luxury jewelry and fashion accessories.
What materials do chainistes use to create chains?
Chainistes typically work with precious metals such as gold, silver, and platinum, though they may also use other materials depending on the design.
How long does it take to become a skilled chainiste?
Becoming a skilled chainiste can take years of training and practice, as the craft requires precision, technical knowledge, and artistry.
What techniques do chainistes use to ensure the strength of chains?
Chainistes use techniques like soldering and careful link assembly to ensure the durability and strength of their chains.
Can chainistes create custom-made chains?
Yes, many chainistes specialize in creating bespoke chains for high-end clients, tailoring their designs to meet individual preferences and styles.
Also Read: Showbizztoday.com: A Hub of Entertainment, Lifestyle, Music and Fashion
Conclusion
The chainiste’s function is just as important now as it was in the past. The traditions of jewelry-making are preserved by these skilled artisans, who also embrace modern innovations to enhance their craft. Chainistes offer a special blend of imagination, accuracy, and technical knowledge to their work, whether they are making one-of-a-kind chains for high-end customers or producing long-lasting pieces in bulk for commercial brands.
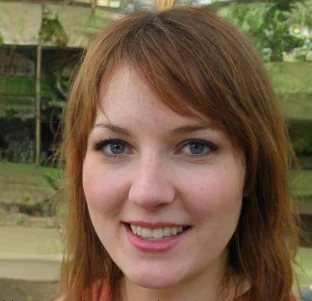
Jennifer Forster is a skilled writer at Explainervilla.com, where she covers a wide range of topics such as technology, lifestyle, and culture. Her work emphasizes how contemporary trends intersect with traditional values, breaking down complex innovations and sustainability initiatives into easy-to-understand insights.